Inventory Management Can Be Fun For Anyone
Table of ContentsInventory Management Fundamentals ExplainedNot known Facts About Inventory ManagementThe smart Trick of Inventory Management That Nobody is DiscussingThe Only Guide to Inventory Management
There are 2 primary methods of tracking supply: routine and perpetual. The primary distinction between these is how typically information is updated. Despite how usually you track stock, you may intend to use among the adhering to supply administration techniques: ABC Analysis, ABC (Always Better Control) Analysis is inventory administration that separates various products right into 3 classifications based upon prices and is separated right into groups A, B, or C.The items in the B category are reasonably more affordable compared to the A classification. As well as the C group has the least expensive products of all 3. EOQ Design, Economic Order Quantity is a technique made use of for planning and purchasing an order amount. It entails making a choice regarding the quantity of inventory that should be put in supply at any type of offered time. Inventory Management.
FSN Approach, This technique of supply control describes the process of monitoring all the items of stock that are not made use of often or are not required at all times. They are after that classified into three different groups: fast-moving inventory, slow-moving supply, as well as non-moving stock. JIT Approach, In the nick of time stock control is a procedure made use of by suppliers to regulate their inventory degrees.
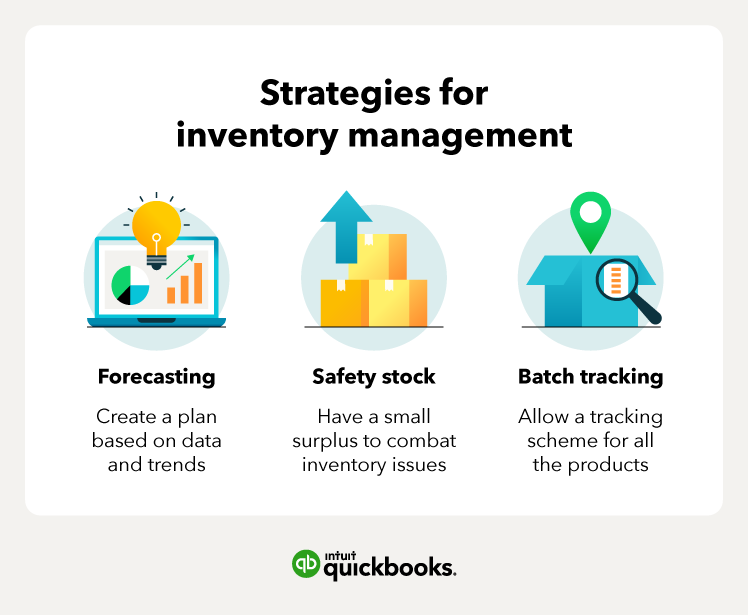
The smart Trick of Inventory Management That Nobody is Discussing
VED Evaluation, VED is a method used by organizations to manage their inventory. It mostly relates to the administration of crucial and preferable spare components. The high degree of stock that is needed for production usually justifies the low supply for those parts. Among the most crucial variables that a company need to consider is the accuracy of the details provided in its supply databases.
Wrike is a job administration service that can aid you do precisely that. With Wrike's product administration tools, you can manage all of your item group's tasks in one place as well as get the most out of every project. Wrike's product launch automation aids accelerate item launches with a streamlined method.

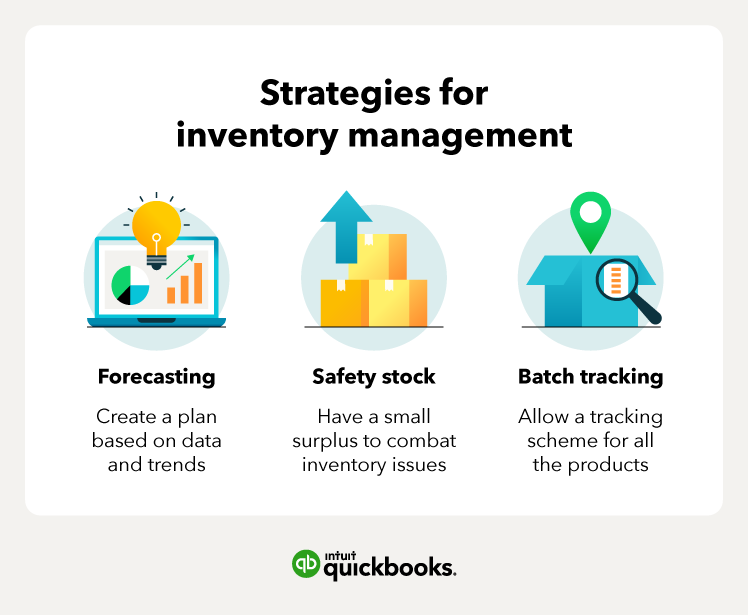
The Greatest Guide To Inventory Management
Supply management describes the process of getting, saving, making use of, and also offering a business's stock. This includes the management of resources, elements, as well as completed products, in click reference addition to warehousing and also processing of such items. There are different sorts of supply monitoring, each with its benefits and drawbacks, relying on a business's requirements.
Stock management attempts to effectively streamline inventories to stay clear of both gluts and scarcities. 4 major supply management techniques include just-in-time monitoring (JIT), materials need preparation (MRP), financial order quantity (EOQ), and also days sales of inventory (DSI). There are advantages and disadvantages per of the techniques, evaluated below. A company's supply is one of its most beneficial assets.
A shortage of stock when and also where it's required can be very harmful (Inventory Management). At the very same time, supply can be thought of as a liability (otherwise in an accountancy feeling). A huge inventory brings the threat of spoilage, theft, damage, or shifts in need. Inventory should be insured, and also if it is not marketed in time it may have to be gotten rid of at clearance pricesor merely destroyed.
Understanding when to replenish supply, what quantities to buy or create, what rate to payas well as when to market and also at what pricecan conveniently ended up being complicated choices. Small companies will certainly often track supply by hand as well as figure out the reorder factors and also quantities utilizing spread sheet (Excel) solutions. Larger organizations will certainly utilize specialized enterprise resource planning (ERP) software.
Inventory Management Things To Know Before You Buy
Ideal inventory administration methods index vary depending upon the sector. An oil depot is able to save big amounts of stock for extensive time periods, allowing it to await demand to grab. While saving oil is pricey as well as riskya fire in the U.K. in 2005 brought about numerous pounds in damage as well as finesthere is no threat that the inventory will spoil or head out of design.
For business with intricate supply chains and producing procedures, stabilizing the risks of inventory excess and scarcities is especially tough. To accomplish these balances, firms have established a number of methods for stock administration, consisting of just-in-time (JIT) as well as materials demand planning (MRP). Some business, such as monetary services firms, do not have physical supply and also so needs to depend on more helpful hints solution procedure monitoring.
Inventory has to be physically counted or measured prior to it can be placed on an annual report. Companies typically maintain innovative supply monitoring systems efficient in tracking real-time stock levels. Supply is made up making use of among 3 methods: first-in-first-out (FIFO) costing; last-in-first-out (LIFO) costing; or weighted-average setting you back. A supply account generally contains 4 different categories: Resources represent various products a business purchases for its production procedure.
Operate in process (additionally known as goods-in-process) stands for raw products in the process of being changed right into a completed item. Finished items are completed products easily offered up for sale to a company's customers. Goods stands for completed goods a business acquires from a vendor for future resale. Relying on the kind of organization or item being assessed, a business will utilize numerous inventory monitoring methods.